Filling Lines
Let’s work together to create tailored filling solutions that meet your manufacturing needs. Our filling lines cater to various industries, whether for small or large-scale production!
VITOPACK Filling Lines
With over 15 years of extensive expertise, we specialize in manufacturing complete filling lines. We take pride in designing and building filling solutions that cater to the unique needs of both small and large businesses across various industries.
In addition to our standard filling lines, such as sauce and medical filling lines, we offer customized solutions tailored to your production requirements. From emulsifying machines and mixing tanks to filling, capping, sealing, labeling, and case packing machines, we provide a comprehensive production line to meet all your needs.
-1024x295.png)
Sauce Filling Line
Complete filling line for liquid food production (sauce, honey, mayonnaise, jams, etc.) Emulsifying machine, mixing tank, filling machine, capping/sealing machine, labeling machine, case machine.
new-size-1024x295.png)
Pharmaceuticals Filling Line
Complete filling line for various medical production (liquids, tablets, powder,inhalers, glass vials, cartridges, syringes etc.) lsolator system, washer,depyrogenation tunnel, filling machine,capping/sealing machine, labelingmachine, case machine.
Our Filling Line Advantages
Tailored Solutions
Our filling lines are designed to accommodate various product viscosities, ensuring efficient filling for both low and high-viscosity liquids. This adaptability allows us to meet the unique needs of your products.
Versatile Compatibility
We offer filling lines that cater to different bottle and container types, ensuring a perfect fit for your packaging needs. Whether you have standard bottles or custom shapes, we have the right solution for you.
High Efficiency and Speed
Our fully automatic filling lines are engineered for high-speed production, allowing you to fill more bottles per minute compared to semi-automatic options. This efficiency helps streamline your operations and boost productivity.
Quality and Durability
Constructed from high-quality stainless steel, our filling lines meet international quality standards, ensuring longevity and reliability. This commitment to quality not only protects your products but also enhances the overall efficiency of your manufacturing process.
What Are Filling Lines?
Packaging products, particularly liquids and chemicals, necessitates careful handling during the filling process. The method used can vary based on the type of product being packaged and the packaging materials involved, such as PET or glass bottles, cans, or Tetra-packs. Each stage of a filling line requires a distinct set of machinery to achieve specific objectives effectively.
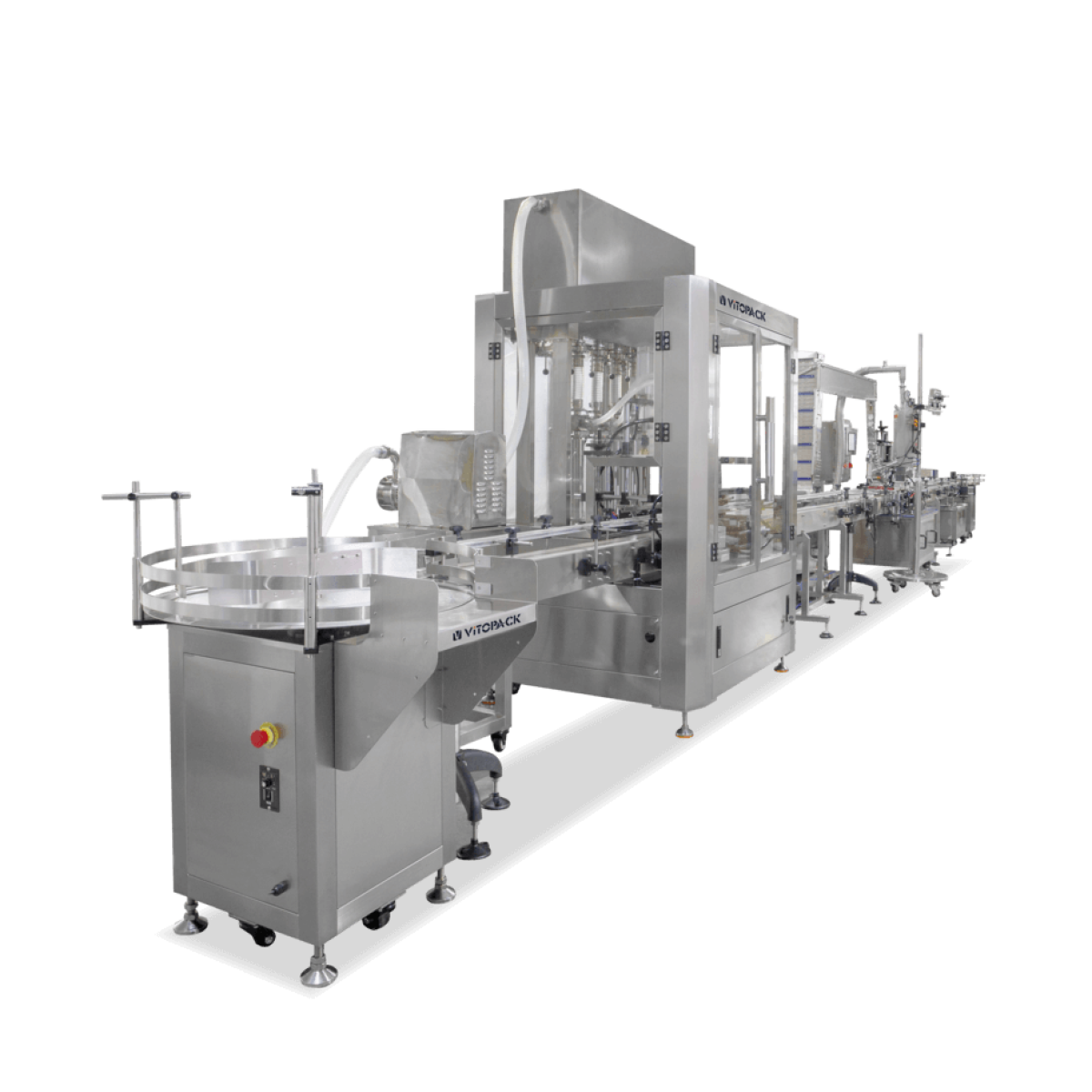

Filling Line Features:
- One of the most innovative and competitively priced bottle filling lines available today.
- High productivity with reduced labor costs.
- Customized integration services tailored to meet the needs of various products.
- No need for replacement parts; all contact components can be disassembled without tools.
- Compliance with cGMP standards.
- Feeding trays equipped with dual levels of vibration.
- Separate hoppers and vibrating components on the channel counter.
- Dual-lane, standard hygienic conveyor system.
- Constructed from high-quality stainless steel.
- Comprehensive training and support for onsite integration, setup, and installation.
Filling Lines Workflow:
- Product processing/making system
- Bottle/container feeding
- Automatic product filling
- Automatic cap feeding
- Automatic aluminum foil sealing
- Automatic bottle labeling
- Automatic inkjet date printing
- Finished product collection table
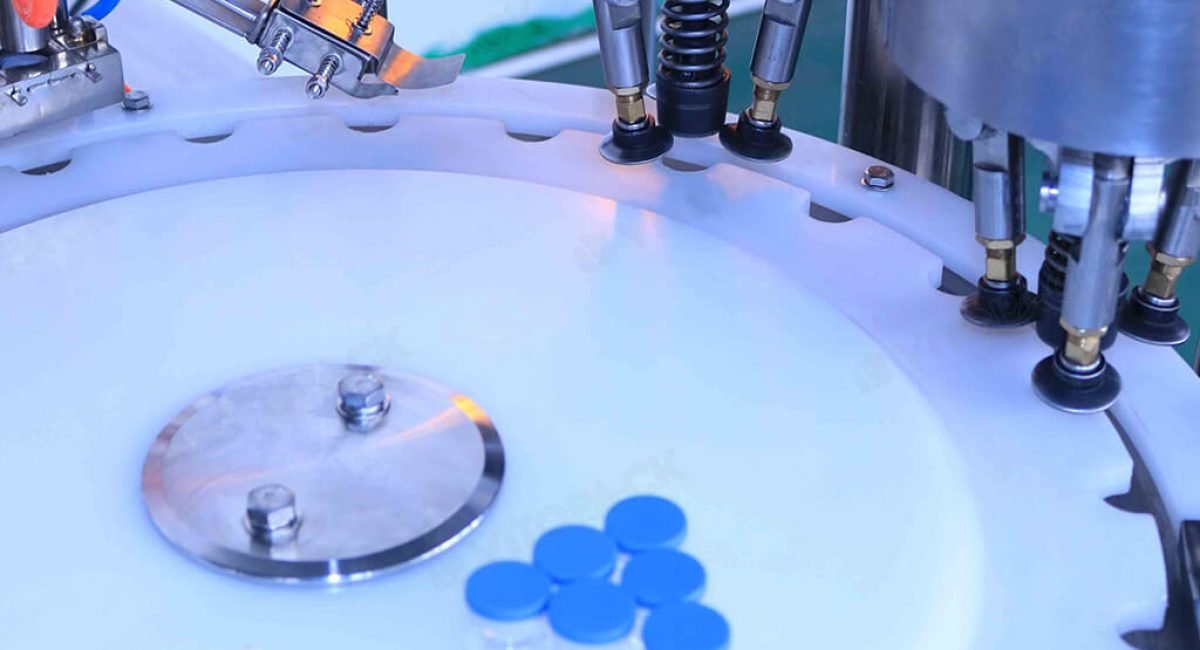
What are the Components of the Filling Line?
A filling line consists of multiple components that work together seamlessly. While these components may vary from manufacturer to manufacturer, they share the same fundamental parts. These elements include:
Emulsifying Machine : This device is designed to mix the product’s liquid and dry ingredients into a fine, consistent, and flavorful mixture.
Mixing Tank : This stainless steel mixer features an automated liquid level control system with precise proportional flow control and temperature regulation. It is designed for CIP Clean−In−Place cleaning systems without dead angles.
Holding Area : This section holds the empty bottles that will be used for filling the product.
Bottle Feeder : This component places the bottles in position, ready for filling.
Electrical Unit : All electrical components necessary to operate the filling line are contained within this unit. Additionally, it powers the machine’s control panel, where the machine’s control components are located. The operator can monitor the filling procedure and input parameters from this panel.
Motors : These components convert electrical energy into mechanical energy, powering the filling line’s mechanical actuators.
Product Filling Unit : This section is used for filling the product into bottles or other packaging.
Pump Filler : This pump fills the bottles by directing the product to the filling heads, controlling the amount of liquid that enters each bottle.
Sensors : These devices facilitate the filling process by identifying the presence of bottles during filling. They help reduce waste by preventing the system from filling bottles if none are detected at the filling station.
Filling Station : This machine station is specifically designed for filling products into bottles.
Filling Heads : These assist in filling multiple bottles throughout the assembly process.
Capping Device : After the filling process, this device attaches caps to the bottles.
Bottle Support : This support keeps the bottles in place during the filling procedure to ensure precision.
Conveyor Belt : This component guides the bottles as they move through the filling process.
Product Labeler : The labeling machine applies labels to products or packaging.
Case Packing : The case packing machine loads finished products from a tray or wraparound case’s side, top, or bottom. After loading the goods, the case is closed and sealed with glue or tape.
Boost the Quality and Efficiency of Your Filling Line
What are the Factors to Consider When Choosing a Filling Line?
Selecting a suitable filling line is crucial, and several factors must be taken into account. The right filling and capping machine will ensure efficient product filling. Here are some key considerations before making a selection:
Product Viscosity : Viscosity refers to a product’s resistance to flow. Liquids with lower viscosity flow more quickly, while those with higher viscosity move more slowly.
Filler Type : The filler component is essential for maintaining a steady fill rate. It can be either pulse-based or time-based, depending on your filling requirements.
Bottle/Container Type : The ideal filling line for your business will depend on the size and shape of your bottles or containers.
Filling Rate : Estimate the number of bottles you want to fill per minute. Fully automatic filling lines can fill more bottles in a given time compared to semi-automated lines, but they are typically more expensive.
Filling Volume : You can use a liquid-level process, a volumetric process, or spiral feeding and light control technology to fill the bottles accurately.
Holding Tank : Ensure that the storage tank can hold a sufficient quantity of liquid products without requiring frequent refills. This will allow for faster filling.
Quality Standards : It is crucial to choose a filling line that complies with international quality standards. These measures protect both workers and the final products, ensuring the efficiency, efficacy, and marketability of the manufacturing process.
Machine Body Material : Opt for stainless steel for the filling line, as it guarantees high performance and a long lifespan.
Budget : Your financial situation will determine how much you can afford to spend on a filling line. Select a filling line that aligns with your current production level.
Technological Advancement : Technology is constantly evolving. The efficiency of a filling line depends on the level of technology it employs. Recent advancements have made improved filling methods possible.
Efficiency : Invest in a filling line that ensures effective filling every time.
Machine Configuration : Filling lines come in various types and sizes. Choose one that fits your workspace well. Larger spaces are typically required for commercial filling lines compared to home-based setups.
Maintenance : A filling line that is easy to repair can benefit your business if issues arise. Ensure that replacement components are readily available to minimize delays during the filling operation.
What are the Benefits of Automatic Filling Lines?
Control Panel : An automated filling line features an intuitive user interface, complete with visible knobs and indicators. By simply pressing a button on the control panel, the machine becomes easier to operate, which also reduces the likelihood of operator accidents.
Automation : Filling lines can be either fully or semi-automatic, meaning they can operate with little to no supervision from operators. Once the parameters for operation are set, the only task left is to monitor the machines as they perform their functions.
Production Capacity : Automatic filling equipment offers fast filling speeds, which significantly reduces manual effort. This capability allows for the completion of multiple orders quickly.
Design : Automatic filling lines typically have a compact footprint, enabling flexibility and easy installation. They can be easily integrated into industrial settings without requiring a large amount of space.
Material Quality :The materials used in the fabrication of filling lines are primarily stainless steel or aluminum. These materials not only possess anti-corrosive properties but are also durable, minimizing the likelihood of needing to replace equipment over time and ultimately saving costs.
What Quality Standards Should Filling Lines Adhere To?
To ensure consumer safety, a filling line must comply with all applicable international quality standards. Key benchmarks include:
Current Good Manufacturing Practice cGMP : A filling line must adhere to the following cGMP standards:
- Maintain consistency throughout production.
- Meet or exceed all applicable international specifications.
- Develop effective methods for filling.
Restriction of Hazardous Substances RoHS : This standard aims to reduce adverse effects on the environment and human health. It ensures that the equipment does not produce dangerous substances during operation.
European Union CE Marking : While this standard pertains specifically to the European Economic Area, it is recognized by businesses worldwide.
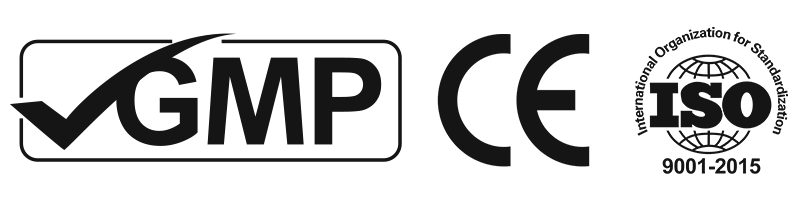
Get instant Quote
Instant Quotes Tailored for You!
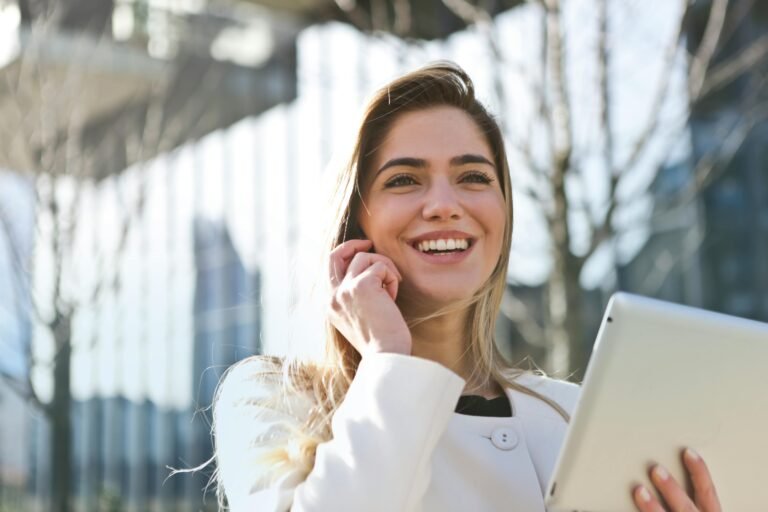